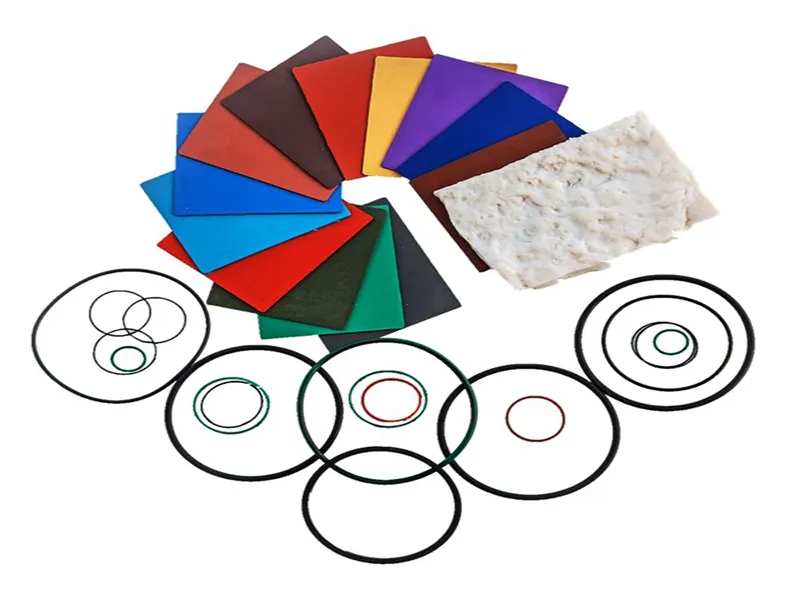
Our facility is equipped with a Class 100,000 cleanroom production line and seven automated production lines, with an annual capacity of 2,500 tons, ensuring reliable production for various industrial applications.
Our facility is equipped with a Class 100,000 cleanroom production line and seven automated production lines, with an annual capacity of 2,500 tons, ensuring reliable production for various industrial applications.
Hydrogenated nitrile rubber (HNBR) is a highly saturated elastomer derived from nitrile rubber (NBR) through a specialized hydrogenation process. This modification enhances its flexibility, durability, and resistance to heat, oil, and chemicals, making it suitable for demanding environments. HNBR can be processed into various forms, including O-rings, sealing gaskets, and rubber hoses, to meet the specific needs of industrial, automotive, and oilfield applications. Its adaptability and strong mechanical properties make it a reliable material for sealing and fluid transfer solutions in harsh operating conditions.
Hydrogenated nitrile rubber (HNBR) is widely used in industries that demand durability, resistance to extreme conditions, and long-term reliability. Its ability to withstand high temperatures, chemical exposure, and mechanical stress makes it a preferred material for various applications.
HNBR is used in fuel tanks, seals, fuel pump diaphragms, and valve linings, providing resistance to heat, oil, and contaminants commonly found in engine compartments. These properties enhance the durability of automotive components, ensuring long-term performance and vehicle safety.
Designed for deep well drilling seals, wellhead gaskets, drill pipe protectors, and packers, HNBR withstands high temperatures, pressure, and exposure to acids and amines. Its resilience ensures leak-free operations and extended service life for critical oilfield equipment.
Used in aircraft seals, fuel bladders, and hydraulic tubing, HNBR ensures reliable operation in extreme temperature fluctuations and high-radiation environments. Its stability under harsh conditions contributes to the safety and performance of aerospace components.
As an insulation material for circuit boards and electronic components, HNBR provides protection against moisture and short circuits. Its soft and flexible nature prevents damage to delicate parts, ensuring the longevity and reliability of electronic devices.
HNBR is widely applied in seals, vibration dampening components, and rubber rollers, helping to improve sealing efficiency, reduce equipment wear, and enhance mechanical stability. Its resilience minimizes downtime and maintenance costs, extending the lifespan of industrial machinery.
Product Code | Specific Gravity (g/cm³) | Hardness (Shore A) | Tensile Strength, Ultimate (MPa) | Elongation at Break (%) | Compression Set (%) | TR10 Low Temperature Resistance (℃) | Applications |
| 1. 16±0.03 | 50±5 | 19 | 434 | 23 | -24 | O-rings, gaskets, and simple structural components |
| 1. 19±0.03 | 55±5 | 17 | 330 | 19 | -24 | |
| 1.22±0.03 | 60±5 | 19.6 | 392 | 22 | -24 | |
| 1.24±0.03 | 60±5 | 17 | 320 | 22 | -24 | |
| 1.26±0.03 | 65±5 | 23 | 289 | 21 | -24 | |
| 1.26±0.03 | 65±5 | 20 | 288 | 18 | -24 | |
| 1.31±0.03 | 70±5 | 19 | 300 | 19 | -24 | Complex structural components |
| 1.24±0.03 | 70±5 | 21 | 250 | 20 | -24 | O-rings, gaskets, and simple structural components |
| 1.26±0.03 | 70±5 | 20 | 255 | 26 | -21 | Complex structural components |
| 1.27±0.03 | 75±5 | 22 | 230 | 24 | -21 | O-rings, gaskets, and simple structural components |
| 1.33±0.03 | 75±5 | 22 | 260 | 19.6 | -20 | |
| 1.29±0.03 | 75±5 | 22 | 260 | 19 | -22 | Complex structural components |
| 1.29±0.03 | 75±5 | 21 | 270 | 18.5 | -22 | |
| 1.36+0.03 | 80±5 | 22 | 210 | 17.7 | -21 | O-rings, gaskets, and simple structural components |
More HNBR compounds are available. Please contact our technical team to identify the right materials that meet your specific application and performance requirements.
With tensile strength ranging from 10MPa to 30MPa and elongation at break between 200% and 800%, HNBR is designed to handle significant mechanical stress without cracking or wearing down. Its high tear and abrasion resistance ensures reliable performance in dynamic applications, even under continuous use.
HNBR stands up to fuel, lubricants, and aromatic solvents, making it ideal for automotive and industrial sealing applications. It also offers excellent chemical resistance, maintaining its properties when exposed to freon, acids, alkalis, and other corrosive substances. Additionally, its ozone and weather resistance allows for long-term use in outdoor and high-exposure environments.
This material features a smooth, uniform texture with a modulus of elasticity between 1MPa and 10MPa, allowing it to conform to sealing surfaces for a secure fit. Its flexibility and structural integrity make it suitable for precision applications where performance and appearance are both critical.
HNBR maintains its performance across a broad temperature range of -55°C to 180°C, making it suitable for high-temperature automotive engine compartments as well as low-temperature environments in colder climates. This balance of heat and cold resistance ensures consistent reliability across diverse applications.
Our HNBR compounds meet IATF 16949:2016 quality management standards and comply with ASTM D2000 and ISO 6471, ensuring compatibility with international industry requirements. These certifications validate its reliability for demanding industries, including automotive, aerospace, and heavy machinery.
Our standard packaging includes 25kg per container, but we also offer customized options based on specific bulk order requirements. Various packaging formats, such as large and small packages, as well as palletized solutions, are available to facilitate storage and transportation. Let us know your needs for a tailored solution.
We utilize advanced mixing, vulcanization, and processing techniques to ensure precise control over key parameters such as temperature, processing time, and curing pressure. Our expertise in compression molding, extrusion, and injection molding allows us to produce customized shapes and sizes, meeting diverse application requirements across industries.
We offer technical consultation to help customers choose the most suitable HNBR compound based on their specific application and performance requirements. Our team works closely with clients to develop custom formulations, optimizing material properties to meet unique technical challenges. Beyond product development, we provide ongoing support through a structured after-sales service system. This includes tracking product performance, addressing any issues that arise during use, and delivering timely solutions to ensure smooth integration into manufacturing processes. Our goal is to help customers maximize efficiency and reliability in their applications.
HNBR is known for its exceptional oil resistance, maintaining its properties even when exposed to various fuel and lubricant types. It also offers high heat resistance, allowing it to perform reliably at elevated temperatures for extended periods. In addition, HNBR exhibits strong chemical resistance, making it suitable for environments where exposure to acids, bases, and other reactive substances is common. Its high tensile strength and tear resistance ensure durability under mechanical stress, making it a preferred material for applications that require long-term reliability and resistance to wear and deformation.
HNBR can operate reliably within a temperature range of -20°C to 150°C under normal conditions. However, with specialized formulations and processing, it can withstand even higher temperatures for short durations, making it well-suited for applications exposed to thermal cycling or extreme heat environments.
HNBR is widely used across multiple industries due to its combination of heat, oil, and chemical resistance. In the automotive industry, it is commonly found in seals, gaskets, fuel hoses, and other engine components that need to withstand oil exposure and high operating temperatures. The petrochemical sector relies on HNBR for seals and pipeline components that resist harsh chemicals and extreme conditions. Additionally, in the aerospace industry, HNBR is used in fuel system seals, hydraulic components, and protective coverings, where maintaining material integrity in extreme environments is critical.
If an electronic device operates in an environment where oil contamination is a concern or requires heat resistance, HNBR can be a suitable choice. It provides protection against oil exposure while maintaining sealing integrity within its temperature range. This helps safeguard sensitive electronic components from external contaminants, ensuring reliable performance over time.
We follow a strict quality control process that begins with careful raw material selection and extends through each stage of production. Every step is closely monitored by specialized personnel to ensure consistency and reliability. Our HNBR products comply with international industry standards, and we continuously refine our formulations to improve durability, performance, and adaptability to evolving industry demands.
Under normal production conditions, our lead time is 10 business days. However, if there are raw material supply constraints or a sudden increase in orders, we proactively communicate with customers to ensure timely delivery and efficient production scheduling to meet specific requirements.
Feel free to reach out to us for any inquiries.
We specialize in the research and production of rubber compounds and industrial rubber products. With over 30 years of expertise in rubber compounding, our R&D team has in-depth knowledge in polymer materials, chemistry, and other technical fields, providing strong support for the development of specialized rubber materials.
We provide specialty rubber solutions for a wide range of industries, including automotive, semiconductor manufacturing, oil and gas, aerospace, and wearable technology. Each sector presents unique challenges, from high-temperature resistance and chemical exposure to precision sealing and mechanical durability.